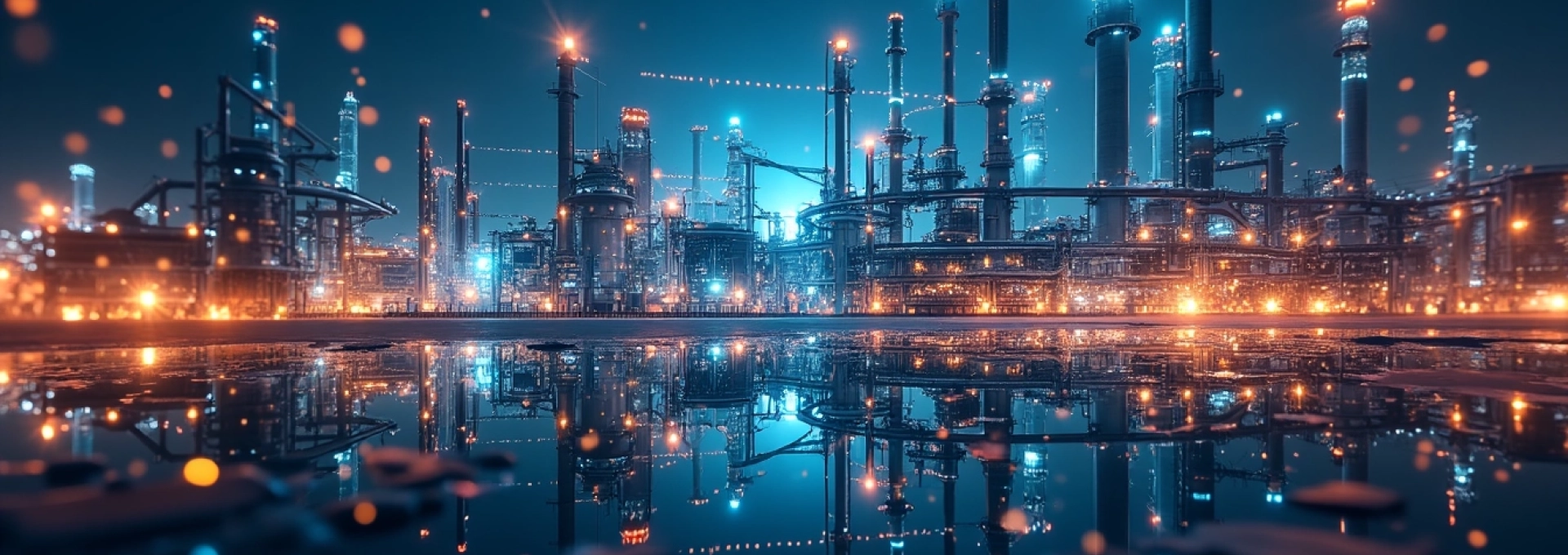
L'industrie moderne fait face à un défi de taille : optimiser sa production tout en réduisant son empreinte énergétique. Les équipements industriels ultra-modernes à faible consommation énergétique représentent une solution incontournable pour relever ce défi. Ces technologies de pointe permettent non seulement de réaliser des économies substantielles, mais aussi de répondre aux exigences croissantes en matière de développement durable. Des moteurs haute performance aux systèmes d'automatisation intelligents, en passant par les solutions de récupération d'énergie, une nouvelle ère s'ouvre pour l'industrie, conjuguant efficacité opérationnelle et responsabilité environnementale.
Technologies de pointe pour l'efficacité énergétique industrielle
L'efficacité énergétique est devenue un enjeu majeur pour les industries du monde entier. Face aux pressions économiques et environnementales, les entreprises se tournent vers des technologies innovantes pour optimiser leur consommation d'énergie. Ces avancées technologiques permettent non seulement de réduire les coûts opérationnels, mais aussi de minimiser l'impact environnemental des activités industrielles.
Parmi les innovations les plus prometteuses, on trouve les systèmes de gestion de l'énergie basés sur l'intelligence artificielle. Ces plateformes analysent en temps réel les données de consommation et ajustent automatiquement les paramètres de production pour maximiser l'efficacité énergétique. Selon une étude récente, l'implémentation de tels systèmes peut entraîner une réduction de la consommation d'énergie allant jusqu'à 20% dans certains secteurs industriels.
Une autre technologie révolutionnaire est celle des matériaux intelligents utilisés dans la conception des équipements industriels. Ces matériaux peuvent changer leurs propriétés en fonction des conditions environnantes, permettant par exemple une meilleure isolation thermique ou une conductivité électrique optimisée selon les besoins. L'utilisation de ces matériaux dans la fabrication de fours industriels a permis de réduire la consommation d'énergie de 15% tout en améliorant la qualité des produits finis.
Systèmes d'automatisation et de contrôle avancés
Les systèmes d'automatisation et de contrôle avancés jouent un rôle crucial dans l'optimisation de la consommation énergétique des installations industrielles. Ces technologies permettent une gestion fine et précise des processus de production, éliminant les gaspillages et maximisant l'efficacité opérationnelle.
Plateformes SCADA nouvelle génération
Les plateformes SCADA (Supervisory Control and Data Acquisition) de nouvelle génération représentent une avancée significative dans le domaine de l'automatisation industrielle. Ces systèmes offrent une vue d'ensemble en temps réel de l'ensemble des opérations, permettant aux gestionnaires de prendre des décisions éclairées pour optimiser la consommation d'énergie.
Les SCADA modernes intègrent des fonctionnalités avancées telles que la visualisation 3D des processus, l'analyse prédictive des pannes, et la gestion intelligente des alarmes. Grâce à ces outils, les opérateurs peuvent anticiper les pics de consommation et ajuster proactivement les paramètres de production pour maintenir une efficacité énergétique optimale.
Intégration de l'intelligence artificielle dans les processus
L'intelligence artificielle (IA) révolutionne la manière dont les industries gèrent leur consommation énergétique. Les algorithmes d'IA analysent des quantités massives de données opérationnelles pour identifier des modèles de consommation et suggérer des optimisations en temps réel.
Par exemple, dans une usine de production automobile, un système d'IA a permis de réduire la consommation d'énergie des robots de soudure de 12% en optimisant leurs mouvements et leurs temps de pause. Cette intégration de l'IA dans les processus industriels ouvre la voie à une nouvelle ère d'efficacité énergétique.
Capteurs IoT pour une surveillance en temps réel
Les capteurs IoT (Internet of Things) constituent la colonne vertébrale des systèmes d'automatisation modernes. Ces dispositifs miniaturisés collectent en continu des données sur la consommation d'énergie, la température, la pression, et d'autres paramètres critiques.
Grâce à ces capteurs, les industries peuvent mettre en place une surveillance granulaire de leur consommation énergétique. Par exemple, dans une usine de produits chimiques, l'installation de capteurs IoT sur les équipements de distillation a permis de réduire la consommation d'énergie de 8% en identifiant et en corrigeant rapidement les inefficacités du processus.
Optimisation prédictive par machine learning
Le machine learning, une branche de l'intelligence artificielle, permet aux systèmes industriels de s'améliorer continuellement en apprenant des données historiques et des résultats passés. Cette technologie est particulièrement efficace pour l'optimisation prédictive de la consommation énergétique.
Dans une centrale électrique, un système basé sur le machine learning a été capable de prédire avec une précision de 95% les pics de demande énergétique, permettant ainsi une gestion proactive des ressources. Cette capacité de prédiction a entraîné une réduction de 7% de la consommation globale de carburant de la centrale.
L'automatisation intelligente n'est pas seulement une question d'efficacité, c'est un impératif pour la durabilité industrielle du 21e siècle.
Équipements de production à haute performance énergétique
Les équipements de production à haute performance énergétique sont au cœur de la révolution de l'efficacité dans l'industrie moderne. Ces technologies innovantes permettent de réduire significativement la consommation d'énergie tout en maintenant, voire en améliorant, la productivité et la qualité des produits.
Moteurs électriques à rendement premium IE4
Les moteurs électriques sont omniprésents dans l'industrie et représentent une part importante de la consommation énergétique globale. Les moteurs à rendement premium IE4 constituent une avancée majeure dans ce domaine. Ces moteurs offrent un rendement énergétique supérieur à 95%, ce qui se traduit par des économies substantielles sur le long terme.
Une étude de cas dans une usine textile a montré que le remplacement des anciens moteurs par des modèles IE4 a permis de réduire la consommation d'électricité de 15% tout en augmentant la durée de vie des équipements. L'investissement initial plus élevé a été amorti en moins de deux ans grâce aux économies réalisées.
Systèmes de récupération de chaleur industrielle
La récupération de chaleur est un domaine où les gains en efficacité énergétique peuvent être spectaculaires. Les systèmes modernes de récupération de chaleur industrielle permettent de capturer et de réutiliser l'énergie thermique qui serait autrement perdue dans l'environnement.
Dans une aciérie, l'installation d'un système de récupération de chaleur sur les fours de traitement thermique a permis de réduire la consommation de gaz naturel de 30%. La chaleur récupérée est utilisée pour préchauffer l'air de combustion et pour alimenter le système de chauffage des bâtiments, créant ainsi une synergie énergétique au sein de l'usine.
Compresseurs d'air à vitesse variable
Les compresseurs d'air sont des consommateurs d'énergie importants dans de nombreuses industries. Les compresseurs à vitesse variable représentent une innovation majeure dans ce domaine. Contrairement aux compresseurs traditionnels qui fonctionnent en tout ou rien, ces modèles ajustent leur vitesse en fonction de la demande réelle d'air comprimé.
Une usine de fabrication automobile a remplacé ses anciens compresseurs par des modèles à vitesse variable, réalisant ainsi une économie d'énergie de 35% sur ce poste. De plus, la qualité de l'air comprimé s'est améliorée, réduisant les risques de défauts de production liés à la condensation.
Fours industriels à isolation thermique avancée
Les fours industriels sont parmi les équipements les plus énergivores dans de nombreux secteurs. Les technologies d'isolation thermique avancée, telles que les matériaux céramiques haute performance et les fibres réfractaires, permettent de réduire considérablement les pertes de chaleur.
Dans une usine de production de verre, l'installation d'un nouveau four équipé d'une isolation thermique de pointe a permis de réduire la consommation d'énergie de 20% tout en augmentant la capacité de production de 15%. Cette amélioration a non seulement réduit les coûts énergétiques mais a également contribué à une meilleure qualité du produit final.
Solutions d'éclairage LED industriel intelligent
L'éclairage représente une part non négligeable de la consommation énergétique dans les environnements industriels. Les solutions d'éclairage LED intelligentes offrent une opportunité unique de réaliser des économies substantielles tout en améliorant les conditions de travail.
Les LED industrielles modernes consomment jusqu'à 75% moins d'énergie que les éclairages traditionnels tout en offrant une durée de vie nettement supérieure. Mais l'innovation ne s'arrête pas là. Les systèmes d'éclairage intelligents intègrent des capteurs de présence et de luminosité qui ajustent automatiquement l'intensité lumineuse en fonction des besoins réels.
Une usine de production alimentaire a implémenté un système d'éclairage LED intelligent et a constaté une réduction de 80% de sa consommation d'énergie liée à l'éclairage. De plus, la qualité de l'éclairage s'est améliorée, contribuant à une meilleure productivité et à une réduction des erreurs de manipulation.
L'éclairage LED intelligent n'est pas seulement une question d'économie d'énergie, c'est un investissement dans la sécurité et le bien-être des employés.
Ces systèmes peuvent également être intégrés aux plateformes de gestion énergétique globale de l'usine, permettant une optimisation encore plus poussée. Par exemple, l'éclairage peut être synchronisé avec les cycles de production, s'adaptant automatiquement aux changements d'équipes ou aux arrêts de maintenance.
Systèmes de stockage et de gestion de l'énergie
La gestion efficace de l'énergie dans l'industrie ne se limite pas à la réduction de la consommation. Les systèmes de stockage et de gestion de l'énergie jouent un rôle crucial dans l'optimisation globale de l'efficacité énergétique industrielle.
Batteries lithium-ion à haute capacité pour l'industrie
Les batteries lithium-ion à haute capacité révolutionnent la manière dont l'industrie gère ses pics de consommation et ses besoins en énergie de secours. Ces batteries offrent une densité énergétique élevée, une longue durée de vie et des temps de charge rapides, les rendant idéales pour les applications industrielles exigeantes.
Dans une usine de production de semi-conducteurs, l'installation d'un système de batteries lithium-ion a permis de réduire la dépendance aux générateurs diesel pour la gestion des micro-coupures. Cette solution a non seulement amélioré la fiabilité de l'alimentation électrique mais a également réduit les émissions de CO2 de l'usine de 15%.
Microgrids intelligents pour sites industriels
Les microgrids intelligents représentent une approche novatrice de la gestion énergétique industrielle. Ces systèmes intègrent des sources d'énergie renouvelables, des dispositifs de stockage et des technologies de contrôle avancées pour créer un réseau électrique local optimisé et résilient.
Un parc industriel a implémenté un microgrid intelligent combinant panneaux solaires, éoliennes et batteries de stockage. Ce système a permis de réduire la dépendance au réseau électrique principal de 40%, tout en assurant une alimentation stable et de qualité pour les industries sensibles du parc.
Logiciels de gestion énergétique prédictive
Les logiciels de gestion énergétique prédictive utilisent des algorithmes avancés de machine learning pour analyser les modèles de consommation, prévoir les besoins futurs et optimiser la distribution de l'énergie en temps réel.
Une raffinerie pétrolière a déployé un système de gestion énergétique prédictive qui a permis de réduire la consommation globale d'énergie de 8%. Le système a identifié des opportunités d'optimisation dans les processus de distillation et de craquage, conduisant à des ajustements qui ont amélioré l'efficacité énergétique sans compromettre la qualité du produit.
Intégration des énergies renouvelables en milieu industriel
L'intégration des énergies renouvelables dans les processus industriels représente une étape cruciale vers la décarbonisation du secteur. Cette transition ne se limite pas à l'installation de panneaux solaires ou d'éoliennes ; elle implique une refonte complète de la manière dont l'énergie est produite, distribuée et consommée dans l'environnement industriel.
Les technologies d'intégration avancées permettent aujourd'hui une symbiose entre les sources d'énergie renouvelable et les processus industriels traditionnels. Par exemple, des systèmes de cogénération utilisant la biomasse peuvent fournir simultanément de l'électricité et de la chaleur pour les processus industriels, maximisant ainsi l'efficacité énergétique globale.
Une usine de papier a réussi à intégrer un système de production d'énergie à partir de déchets de bois, couvrant 60% de ses besoins énergétiques. Cette initiative a non seulement réduit les coûts énergétiques de l'usine mais a également valorisé des déchets qui auraient autrement été mis en décharge.
L
'intégration des énergies renouvelables dans le secteur industriel ne se limite pas à réduire l'empreinte carbone ; elle offre également des opportunités d'innovation et de différenciation sur le marché. Des entreprises pionnières ont démontré qu'il est possible de combiner rentabilité et durabilité grâce à une approche holistique de la gestion énergétique.
Par exemple, une grande entreprise agroalimentaire a mis en place un système intégré combinant l'énergie solaire, éolienne et la méthanisation des déchets organiques. Cette approche a non seulement réduit les coûts énergétiques de 40%, mais a également créé une nouvelle source de revenus grâce à la vente du surplus d'électricité au réseau.
L'intégration des énergies renouvelables nécessite souvent des investissements initiaux importants, mais les avantages à long terme sont considérables. Au-delà des économies directes sur les coûts énergétiques, les entreprises qui adoptent ces technologies bénéficient d'une image de marque renforcée, d'une meilleure résilience face aux fluctuations des prix de l'énergie et d'un avantage concurrentiel dans un marché de plus en plus sensible aux questions environnementales.
L'avenir de l'industrie réside dans sa capacité à harmoniser production et durabilité. Les énergies renouvelables ne sont plus une option, mais une nécessité stratégique.
En conclusion, les équipements industriels ultra-modernes à faible consommation énergétique représentent bien plus qu'une simple évolution technologique. Ils incarnent une transformation profonde de l'industrie, alignant performance économique et responsabilité environnementale. Des systèmes d'automatisation intelligents aux solutions de stockage d'énergie avancées, en passant par l'intégration des énergies renouvelables, ces innovations ouvrent la voie à une industrie plus durable, plus efficiente et plus compétitive.
L'adoption de ces technologies n'est pas sans défis, nécessitant souvent des investissements importants et une refonte des processus existants. Cependant, les bénéfices à long terme - qu'il s'agisse de réductions de coûts, d'amélioration de la productivité ou de conformité aux réglementations environnementales de plus en plus strictes - font de cette transition une nécessité stratégique pour toute entreprise industrielle tournée vers l'avenir.
Alors que nous avançons vers un avenir industriel plus vert et plus intelligent, il est clair que les entreprises qui embrasseront ces technologies innovantes seront les mieux positionnées pour prospérer dans un monde où l'efficacité énergétique et la durabilité deviennent des impératifs incontournables.